by Richard Freudenberger, Living Web Farms Resource and Alternative Energy Coordinator
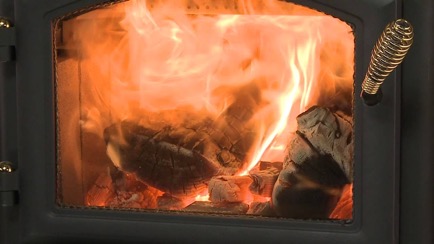
Call it firewood, biomass or solid fuel, it’s still one of the most reliable ways to heat your home—but only if you do it right. Even long-time wood-burners can disagree on what is “right,” so we’re going to do our best to clear the air about best practices in wood burning and selecting appropriate wood-burning stoves.
Getting the most out of firewood is nothing new. Ben Franklin’s heat-radiating stove, Count Rumford’s clean-burning fireplace, and Scandinavia’s wood- frugal tile masonry stoves were all an 18th -Century response to inefficient burning or regional shortages of wood fuel. Enclosed metal and cast-iron stoves followed in the years after, and wood cook stove innovations came close behind, all direct developments of efforts to control temperatures and fuel consumption.
Most of that development went away with the advent of natural gas and electricity, but petroleum shortages and the back-to-the-land movement of the 1970s sparked a renaissance in wood burning which has largely continued to this day.
The Good and Bad of Wood
Wood is a renewable resource that is carbon-neutral when used properly in a certified stove or fireplace insert. Contemporary stoves, with efficiencies of 80 percent or more, make better use of their fuel than most fossil-fuel furnaces and electric resistance heat in any form.
And because wood is a local commodity, there’s no worry about infrastructure, grid stability, scarcity or any of the other risks that come with processed fuels. If you’re fortunate enough to have even small acreage, you can glean your supply on site, from deadfall or proactive management. If not, you can always order a load, split or uncut, and store it pretty much indefinitely if you have it under cover.
But there is a downside. Smoke from residential woodstoves contains an especially damaging pollution called fine particulate matter or PM2.5.– airborne respirable particulates with a diameter of less than 2.5 microns. These super-fine particles in smoke comprise about 93 percent of the smoke’s particulates and can get deep into the lungs, damaging the pulmonary system, blood vessels, and heart.
Other pollutants in smoke include carbon monoxide, volatile organic compounds (VOCs), and benzene. Unregulated residential wood smoke can increase particle pollution to levels that pose serious health concerns, and in some rural areas constitutes a significant portion of the fine particle pollution. More about the health effects of PM2.5 here.
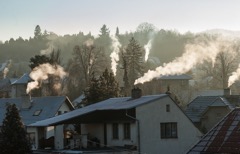
A Brief History of Wood Burning
How we got here from there is an ongoing saga that started with the shift to airtight wood stoves that came with the OPEC fuel crises of the mid-1970’s. Woodstoves now easily account for 75 percent of the cordwood burned in residences, the remainder being fireplaces which are used much less frequently. There are over 11 million homes in the United States that use wood for either primary or secondary heating.
Because the only controls in early airtight stoves were an air inlet and a flue damper, users quickly learned that in order to conserve wood they could throttle down the air inlet and slow the burn once the fire was fully engaged. The result was a smoldering and very dirty fire that would release 40 to 60 grams of particulate matter into the air every hour.
By the 1980’s state agencies and the federal EPA began testing airborne particulates, and in some jurisdictions set wood burning bans on especially bad days. This prompted manufacturers to research and develop clean-air models, which is when the first catalytic and “high-tech” stoves (called non-catalytics) came onto the market.
In 1988 the EPA initiated what would become a three-phase regulation program that required woodstove manufacturers meet a certified emissions standard of 8.5 grams/hr. (5.5 for catalytic models), followed by a 7.5/4.1 gram/hr. standard a few years later. In 2015 that dropped to 4.5 grams/hr. for all certified woodstoves and included previously unregulated outdoor wood boilers, wood furnaces, and pellet stoves. A Phase IV performance standard for 2020 sets the limit at 2.5 grams/hr. for all cordwood burners. Follow this link for information about wood heaters that are in compliance with the 2015 New Source Performance Standard (NSPS) for New Residential Wood Heaters.
So now we’re at an emissions level that’s less than 8 percent of what it was thirty years ago. But just as important we’ve seen efficiencies rise dramatically, so far less fuel is being burned in today’s certified stoves to provide the same amount of heat available from those high-emissions stoves of decades past.
How Wood Burns
The magic happened when designers began looking at the stages of combustion inside the stove. Wood itself doesn’t actually burn. The initial heat source–a match, a coal, burning tinder—decomposes cellulose in the wood starting at about 300 degrees F by breaking chemical bonds between compounds, a thermal decomposition process called pyrolysis. Offgassing of water vapor and volatiles (smoke comprised of oxygen, hydrogen, and carbon) occur at that point, and as temperatures rise to around 540 degrees F, most of the water vapor is driven off, and a large quantity of volatiles are released in a process of primary combustion, which generally occurs below 900 degrees F.
These volatiles, known as secondary gases, contain combustibles such as methane and methanol, along with carbon dioxides and oxides of nitrogen. In order for the secondary gases to burn, temperatures must reach the 1100 degree F range with sufficient oxygen present. These conditions don’t exist in close proximity to the wood because primary combustion is taking up the necessary oxygen.
Secondary combustion is critical to a clean burn and high efficiency and depends on just the right supply of air at high enough temperatures. Too little air cannot support combustion and too much cools temperatures below the needed threshold because its nitrogen absorbs heat.
Left behind is ash and carbon char, which combusts slowly because of the lack of oxygen. With the gases gone from the wood, the carbon chains of cellulose and lignin molecules remain behind as charcoal, which burns for an extended period with a low heat output. This third phase of combustion is still significant because in addition to releasing additional energy which adds to fuel efficiency, the charcoal extends the burn through the night so the fire can easily be reignited with fresh fuel in the morning.
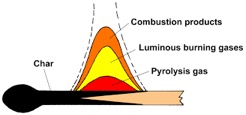
The combustion of wood occurs in varying zones at different temperatures
Two Good Alternatives to a Dirty Burn
Legacy woodstoves, the airtight stoves sold before July 1988, are still in use, either because they are original installations still going strong, or they’ve been sold on the used market as economical buys. As a matter of fact, they are a very poor investment due to their high rate of wood consumption, not to mention a burden on local air quality.
Current certified woodstoves have evolved to include design features that encourage all-important secondary combustion so critical to a complete burn. Popular technologies include the use of catalytic combustors, extended circulation of gases in the stove, controlled secondary air manifolds, baffles, and thermal-mass stove construction to hold heat. More recent entries are smart stoves that use sensors and computer controls to adjust airflow or recycle heated exhaust air.
For most people, clean stoves will fall into two categories—catalytic and non-catalytic. The catalytic types direct exhaust smoke through a ceramic honeycomb catalyst that, when heated to a temperature of around 550 degrees F, burns off volatile gases and strips out particulate matter. Catalytics tend to have a slightly higher efficiency and longer burn times than non-cats, but they can also be a bit more expensive and require more user input. They will not tolerate wet wood, colored or waxed kindling paper, or trash burns of construction waste with nails or wire, as these will inactivate the catalyst unit over time. Even under ideal conditions, the life of a catalyst is limited to ten years or so before it must be replaced.
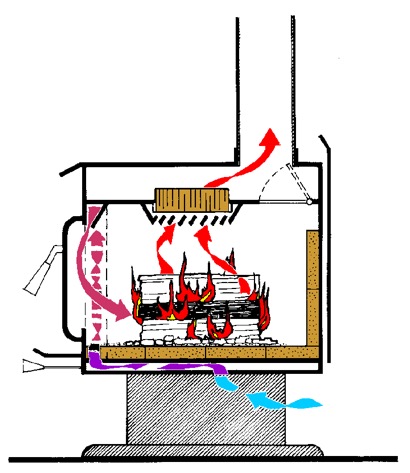
Catalytic woodstoves rely on a coated ceramic honeycomb operating at high temperatures to keep emissions within limits
Non-catalytic stoves depend on internal airflow and delivery to keep secondary burn temperatures in the working range. Internal baffles keep gases in the combustion zone longer to assure a more complete burn and pre-heated air delivery enhances the secondary burn process. The firebox in a non-cat may tend to be smaller because of additional insulation, and its heat output curve may not be as consistent as that of a catalyst type, but the stove requires less user input, and because of the airflow pattern will provide a very visual fire.
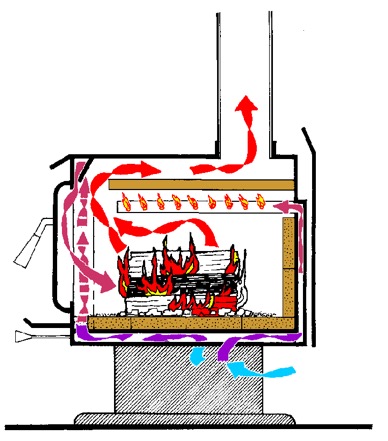
Non-catalytic stoves use flow baffles and a carefully engineered secondary burn manifold to meet emissions standards
At the lowest end of the price scale you may still find non-airtight, ungasketed stoves that are not EPA certified. These were banned from retail sale at the end of 2015, and were only exempt from regulations because they are so leaky that they fall under an 11 lbs./hr. fireplace exemption. Generally they are not UL approved, and are not clean burning by any measure. Their only attraction is their price, and they should be avoided. You can access here The List of EPA Certified wood heaters.
The secret to a good burn in any woodstove is to use only dry, seasoned wood, preferably a hardwood species. Moisture has a significant effect on heat value in the fuel, as uncured wood can have 40 percent lower heat value than wood seasoned to a 19 percent moisture content. It takes, on average, about six months of air-drying in most climates to achieve this level of dryness.