Last time I wrote about controls, things got a little dense real fast. If all of the talk of switches and relays seemed to lack any relevance, then stay put, because this month I’ll skip ahead and show some real concrete examples of ways we use low voltage controls around on our farm. Review the earlier post if you need a refresher on switches and relays. This time, in some real specific examples, I’ll review some of my favorite low cost and versatile control devices we use around Living Web Farms.
But first, remember when working with electricity to take it slow and pay attention to detail. Be redundant with your testing equipment, and know your limits. Depending on your jurisdiction, it may not even be legal for you to work on your own electrical systems (In most cases low voltage controls and appliance repair don’t require licensing) and even though we agree it’s important for owners of their equipment to understand its operation and have the ability to diagnose and repair, we don’t endorse unlicensed or unqualified high voltage electrical work, especially when it puts people and property at risk.
‘Ready-made’ Controllers: Sensor and Switch
Remember a simple control circuit needs three things: a power supply, switch and a load. The switch is either actuated manually – think lightswitch, or your car’s ignition – or automatically, like in your water heater, or refrigerator. Automatic switching devices employ a sensor and some means of reading the sensor, and switch a load accordingly, either directly or through a relay. Sensors and relays are everywhere – as they are the foundation of anything that’s automatically controlled.
Mirroring what I said in last month’s post about switches and relays: refer to a spec sheet when selecting a controller. Look for input voltage requirements, along with amperage switching capabilities. Some controllers are capable of switching relatively high amperage loads directly, others may require an intermediate relay for load switching. Pay attention to environmental ratings – can the controller be used outside, under rain or irrigation? Can it be installed in humid environments? What about memory storage? If it’s an electronic controller, you’ll want to consider whether it can store presets if the power goes out. The list goes on. Again, check the spec sheets and product brochures for these details. Here’s an example before I move on: early on when building out the kiln ventilation system at the biochar facility, we selected a typical household humidity controller for its low cost. We were later disappointed to find we didn’t have the option for remote sensing, or for controlling the humidity outside of the range typical of dwellings – two things we’d have noticed if we paid closer attention to the spec sheets. Four years later now, we’ve learned a bit, but we haven’t lost our spirit for experimentation and finding low cost control options. Following are a few of my low-cost favorites we use around the Living Web Farms Biochar Facility.
TF115 Line Voltage Thermostat
The simple and rugged, affordable PECO TF115 Thermostat comes in a NEMA 4x housing. NEMA ratings correspond to the environment where the unit can be safely operated – 4X is just one of many electrical enclosure ratings. For example, NEMA 1 enclosures are the common interior type that don’t offer much beyond protection from live electrical components, while the NEMA 4 rating states this thermostat has a watertight enclosure: ideal for outdoor locations, greenhouses, or anywhere else it’s likely to get wet.
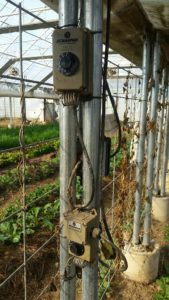
The greenhouses at the Grandview Facility employ TF115 line voltage thermostats to monitor air temperatures and control baffle inflation fans accordingly.
These thermostats use a bimetallic sensor: requiring no outside power source to make or a break a connection between common, and Normally open (N/O) or Normally closed (N/C), based on a user determined dial-set temperature. SPDT operation means it can be used either for heating (where N/O lead has continuity with common, when the actual temp is lower than the set temp) or cooling (where N/O has continuity with common when the temp is higher than the set temp).
The best parts about the TF115 are its rugged housing and simple 120 Vac switching up to 16 amps. Use this when simplicity is preferred over other options like extended remote sensing, or programmable differential. We use these thermostats in our greenhouses to de-energize sidewall and gable baffle inflation blowers when things get too hot.
Ranco ETC
When talking about thermostats, differential refers to the temperature range in between on (switch closed) and off (switch open). Many thermostats use a preset, non-programmable differential somewhere near three degrees, and, for the most part, when heating your homes this is fine. However, in other applications there are a few reasons you might want a more narrow or wider differential. High mass heating loads (think concrete slabs and huge water tanks that require a lot of energy to change temperature) are good at storing and slowly releasing their heat. Radiant floor heating systems are a kind of high mass heating system, where a very low differential is appropriate. On the contrary, low mass heating systems, (or leaky buildings) may require a wider differential to overcome short cycling: where a heating system turns on and off too frequently to maintain a constant temperature.
For these kind of applications I’d look first to the Ranco ETC. This very low cost, easily programmed controller comes in a range of operating voltages, with single and double relay versions available, in a Nema 1 or Nema 4 housing. The simplest version of these controllers has a single relay action, where a circuit is opened when a user determined temperature is realized, and doesn’t close again until the measured temperature is outside of the range of the differential. These controllers have a heating or cooling mode (expressed in the industry as ‘Open on Rise’ or ‘Close on Rise’) that dictates the action of the switch upon rising temperature. Although Ranco controllers don’t offer programmable schedule options like most residential heating thermostats do, and these controllers are limited to one sensor, they’re still one of the most versatile controllers out there. However, r they’re rarely used for human comfort heat; they’re more commonly found in light industrial heating or cooling applications – think temperature control for brewers, walk in coolers, or, in our case for hot water heating control in our curing chamber.
Peltec 102 – Repeat Cycle Timer
The Peltec 102 is an extremely versatile timer relay that absolutely stands out as on my favorites – so much that we’ve installed a few permanently in applications ranging from our chip gasifier agitator control, or for pulsing our biochar retort overheat alarm buzzer. I even keep one around that’s pre-wired for 120V loads. We used it for our irrigation spray bar we used for germination trials last fall. I’m using it now for dialing in the on/off schedule for the pump on our trial aquaponics system.
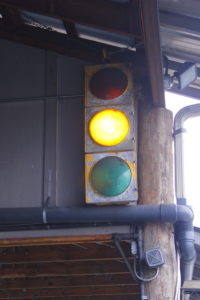
Our overheat and overflow alarm system includes a stoplight and 24V buzzer. When the system gets too hot or condensates aren’t flowing freely, a 24Vac relay energizes the red light and triggers a repeat cycle timer for the buzzer. The yellow light indicates we’re within 100 degrees of overheat.
Just like relays, when you start looking you’ll find that timers are everywhere, and there are so many different types it could make your head spin. We’ve all familiar with countdown timers like the switch on your crock-pot, or the plug-in christmas light timer that operates on a 24-hour cycle. When you see flashing lights at regular intervals, it’s likely a Repeat Cycle Timer that’s responsible. Looking specifically at the Peltec 102 datasheet we find it’s capable of switching up to 16 amps at input voltages from AC/DC 12-240V. What I like most about this one is the separate programmable ON and OFF intervals. For example, I’m not bound to flashing lights for 1 second on/1 second off, now I can use it for controlling our alarm buzzer, where I want 15 seconds off between 1 second on pulses. Or, in the case of our irrigation spray bar, on for 5 minutes with 8 hours in between. I find it especially helpful in experimental applications. Say for some wild reason you wanted something to operate for .1 second every 100 days, then you could do that with this timer.
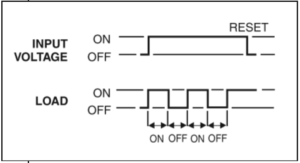
Voltage is applied ‘to the coil’ just like any other relay, and the switching between Common and Normally Open begins at user-programmed intervals. Source: Peltec 102 Spec Sheet
TM-619 Digital Programmable Weekly Timer
Similar in a lot of ways to a Christmas light timer, with a 24 hour cycle, the TM-619 expands on this, allowing for up to 8 different programmable ON/OFF functions over the course of a week. This very low cost unit saves its program when the power flickers, and switches up to 20 amps directly, or can be used to further activate another relay or contactor for large loads. We use one now in our kiln ventilation fan circuit. Process heat from the biochar system keeps the solar wood kiln at a baseline temperature. The solar starts kicking in around 10:00 AM on sunny days and begins boosting temperature, further driving out moisture in the wood. As long as it’s below a set humidity level outside, ventilation fans kick draw in fresh air and exhaust moist air at set intervals throughout the day. This program allows for heat and humidity levels to rise with the sun’s applied heat, then vent, then rise again, and vent again, finally venting again at the end of the solar day.
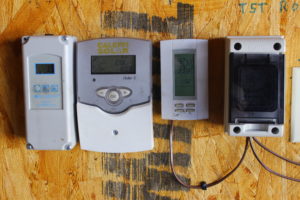
A Ranco, differential controller, humidistat and TM619 timer: working together to help dry sawmill waste before becoming biochar.
PID Resistance Heating
PID stands for proportional-integral-derivative controller, and as you might expect, these things gets incredibly complicated, fast. When applied to resistive heating applications, PID controllers work to maintain a constant temperature by sensing the temperature at the heated device and then anticipating fluctuations by recording rates of change. The PID uses this information to pulse the heater device on and off accordingly. PID technology is used across a wide range of industrial control applications, perhaps most famously as the cruise control function in your car.
We’re using the Inkbird ITC kits with PID, Solid State Relay (you’ll need this kind of relay to allow for rapid switching) and a thermocouple for temperature sensing. These days you can find imported kits like this (albeit with questionable quality)but at very low prices. Lately we’ve been using these on any of our devices that need tight, constant temperature, and are small enough that electrical resistance heating can reasonably do the job. For example, our modified oil burner uses a PID controlled heater at the nozzle for heating waste oils for easier atomization. We use them too, on our extrusion machine from Precious Plastics where we can extrude melted plastic wastes, or even pelleted animal feed.
…and More
The list goes on. We’re using differential temperature controllers normally reserved for solar hot water heating to operate our kiln heater fans. We’ve kept the R8184 ignition control units from our junkyard sourced burners intact for oil burner safety shutoff. Float switches from restaurant equipment have been re-purposed for our condensate collection overflow alarm circuit. A windshield wiper motor (low speed, high torque) powers our small tracking solar array. I’ve even used a pressure switch from a landfill destined dry-cleaning machine for an air cannon that I can shoot off on the Fourth of July or at my kids’ birthday parties. Point is, hopefully now with a little background in what’s out there, you can start to think creatively about what’s possible in low voltage control and automation.