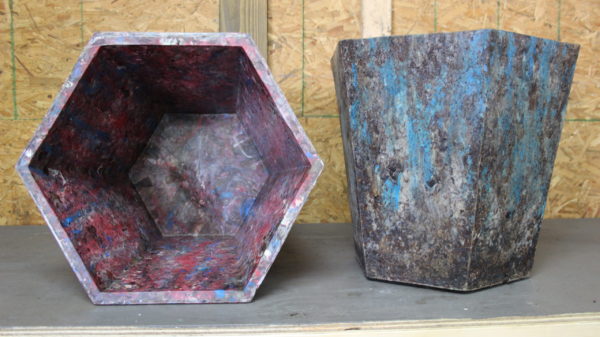
From last year’s Cooking with Food Waste workshop to the upcoming installment of the developing Waste Not series, Living Web Farms is making a point to not only reduce waste, but help change the perspective on waste all together.
There is no waste in nature. As agriculturalists, there is great importance in studying farming practices that mimic natural systems. However, as farmers, it is also important to be honest about certain non-natural materials, particularly plastics, and their role in productive modern sustainable agriculture. Plastics are lightweight, resistant to biological decay, mostly translucent, tough, and most of all, inexpensive. On the farm we use HDPE containers, polystyrene starting trays, PVC piping systems and polyester floating row covers – just to name a few examples. It would be hard to imagine a better suited material than translucent LDPE film for greenhouse coverings; its low cost allows more farmers access to year-around food production. In this sense, plastics could be said to have a democratic “leveling” effect – and, herein lies the problem – agricultural plastics have become so prolific, and so cheap to replace that many farmers and municipalities have implicitly agreed there is little incentive to recycle them when their useful life is over. Without recycling opportunities, the most responsible farmers are left to landfill their plastics. Others bury it on site, or worse yet, burn it. Still, for others, spent agricultural plastics are often piled up and neglected, exposed to UV light and weathering where its size is reduced to unmanageable bits. Perhaps what is most offensive here is our newfound reliance on materials made from petroleum stocks that are formed over millennia, used only for a few seasons, and left behind to degrade for possibly yet another millennium.
For nearly three years the LWF biochar crew has been exploring on-farm plastic recycling. Our doe-eyed naivete humbled and hardened over years of experimentation; Working mostly in fits and starts, what began as a catch-all attempt at processing a wide range of consumer plastics ultimately had us finding our niche at the intersection of contaminated agricultural plastics and biochar production.
Nutrient Cycling
Advocates of a circular economy often describe a dividing line between what they call ‘organic’ and ‘technical nutrients’. Organic nutrients are materials defined by those made from renewable feedstocks and their recycling is governed by biochemical processes – think timber, biofuels or natural fibers for example. A naturally dyed cotton tee shirt can be safely and easily composted whereby it’s nutrients are returned to the soil.
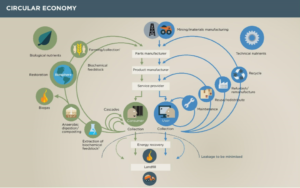
Circular Economy System Diagram from the Ellen MacArthur Foundation
Technical nutrients are materials synthesized from non-renewable materials such as glass, aluminum, steel, or plastics. Ideally, technical nutrients are those that can be continuously recycled without losing integrity. In circular economy models this is realized through leases or refurbishment buyback programs, where products and their various ‘technical nutrients’ are returned to the manufacturer when their useful life is over. On the farm, technical nutrients can be thought of as those that can not be cycled via organic processes – or those that must be repurposed, recycled, incinerated or landfilled when their useful life is over.
This distinction between technical and organic nutrients may seem very mundane – but there are important implications in making these distinctions at home and on the farm. A polyester (technical) and cotton (organic) blend tee shirt CANNOT be responsibly composted at the end of its life. The authors of Cradle to Cradle: Remaking the Way We Make Things warn us about these ‘monstrous hybrids’ of inseparable combinations of both technical and organic nutrients. Coated to-go coffee mugs and PVC/paperboard blister packages are common examples. Wax-coated produce boxes and synthetic ‘latex’ painted plywood are examples of monstrous hybrids one might find on the farm. Lacking foresight, something resembling a monstrous hybrid may be created too – for example, where tangled nylon tomato support strings become frustratingly tangled among the vines, or used LDPE film mulches become contaminated with dirt and moisture beyond the point where conventional recyclers will accept it.
The gardeners at Living Web use durable woven polypropylene landscape fabrics for weed control on specific row crops. Rolled up gently at seasons’ end, and stored away from UV light these fabrics can be expected to last three to five years – at which point these aging fabrics must be removed before their breaking point is realized. Otherwise they will begin to fray, leaving behind strands of the inorganic material, which become increasingly smaller and impossible to remove – effectively creating a ‘monstrous hybrid’ out of our soils.
Reduce, Reuse, Repair, Repurpose, Recycle, Remove
Farmers wishing to reduce their plastic footprint and eliminate pathways to pollution should have a management plan for each type of plastic material used on the farm. It should be simple and for many will sound very familiar. A management plan should include provisions to:
- Reduce future purchases of new material.
- Reuse existing new material to the extent that it remains safe and effective.
- Repair existing material when possible, to further extend its useful life.
- Repurpose existing material when it has exceeded its useful life for its original purpose, so long that it remains safe and effective for its new purpose.
- Recycle existing material when it is no longer useful in its current form
- Remove from circulation the material that is no longer useful, cannot be repurposed and longer safe and is not able to be recycled.
Let’s look at few examples:
Example 1: Polypropylene Weed Barrier
- Reduce: Prioritize robust mulches from organic materials.
- Reuse: Gently remove as soon as possible at seasons’ end. Further extend life by removing loose dirt and storing dry and under cover.
- Repair: Fuse tears and frays by melting ends together with a gentle flame.
- Repurpose: Save short sections for other seasonal projects.
- Recycle: Although it will likely be very challenging to find a recycler to accept the material, your chances are greater by thoroughly removing dirt and water before tightly bounding. Reach out to a local extension agency and see what recycling services are supported in your area.
- Remove: All fabric should be removed from circulation after a field-determined maximum lifespan (five years for us), or when material begins to tear easily and frayed ends become excessive.
Example 2: LLDPE Drip Irrigation Tubing
- Reduce: Use non-plastic or more permanent irrigation techniques when feasible. Purchase robust and reusable 15 mil drip tape when replacing spent lower quality drip tubing.
- Reuse: Gently remove at seasons’ end, flush if necessary and store clean and dry.
- Repair: Inspect for visible damage upon removal and installation. Routinely inspect for leaks throughout the season. Keep repair couplings accessible to field crew.
- Repurpose: Heavier mil drip tapes are tough and allow for many creative uses of short sections.
- Recycle: Until very recently there were markets for used irrigation tapes that were cleaned and baled separately from mulch films. In our own on-farm recycling trials, drip tapes have proven to be one of the best, most consistent and easiest to work materials.
- Remove: Replace aging tapes with higher quality material when leaks appear more consistently and repairs become prohibitively expensive.
Small-Scale Recycling
Recycling – turning used products that would otherwise be discarded as waste and turning them back into useful products – is a complex system of processes with multiple steps, each with its own nuance and challenges. A complete consumer plastics recycling system includes means for Collection, Sorting, Processing, and Forming. On a municipal scale these steps are typically handled by different agencies – collected plastic is sorted and baled at the recycling center, sold to a processor, who then markets the chipped or pelleted raw material to a manufacturer. Our initial on-farm recycling efforts were an attempt to handle all of these processes on our own.
These early efforts were largely inspired by the machine designs from Precious Plastics. Originally a design-school project by dutch artist Dave Hakkens, Precious Plastics has grown into a global network of young and enthusiastic multi-talented plastic-waste problem solvers. At the heart of the movement are open-source plans for mostly DIY low-investment recycling equipment, including a shredder, injection molding and extrusion machines, and various adaptations on compression molding machines. An active online community offers troubleshooting help along with encouragement and advice of all sorts. Nowadays, the precious plastic mission has expanded in scope; included among their offerings now are upgraded semi-industrial machine plans and an online marketplace dubbed the bazar.
By the end of the summer 2017 our crew completed building slightly modified versions of the V2 shredder, injection molding and extrusion machines. The crew’s tenacious fabrication skills combined with a bit of junkyard savvy helped keep fabrication costs extremely low. We were ready to begin experimenting.
Farm staff and families were asked to bring us all of their consumer plastics. Quickly thereafter sorting, de-labeling, washing, shredding, drying and cataloging plastics nearly became a full-time job. Each step had its own challenges, and it was quickly becoming an overwhelming effort that was taking away too much from other responsibilities. After some brief experimentation with PET (#1) and polystyrene (#6) our initial broad collection efforts were quickly limited to only HDPE, LDPE (#2, and #4) and some polypropylene (#5). Even then, reliably sorting polyethylene from polypropylene and subsequent cleaning of equipment after switching between polymers was proving too cumbersome. The following spring, a friend and delivery driver for a local dairy helped us by collecting used, rinsed-out HDPE milk jugs from area restaurants – finally providing for us a steady supply of material that was well-suited for the capabilities of our machines.
Remembering the monstrous hybrid – One of our first hurdles was finding a reasonable way to remove paper labels from hundreds of milk jugs. We attempted solvents, applying heat, scraping and some combination of all three before ultimately settling on cutting them out entirely prior to washing and shredding. Shredded milk jug flakes were laid on screens and allowed to dry overnight before storing for later use. Working within the limitations of our smaller machines, suitable injection molds were designed and fabricated by our incredibly industrious biochar crew. Meanwhile we continued to collect brightly colored HDPE laundry and shampoo bottles when offered. A combination of modest amounts of colored flakes with the translucent white flakes from milk jugs yields fascinating swirl patterns in injection molded products.
Precious Plastics is doing important work and has rightfully gained the attention of an international audience. Where plastic products are generally thought of as mass-produced and cheap throwaway items, the community at Precious Plastics is helping change the narrative about waste. By empowering people around the world to craft unique and beautiful products on machines they can make themselves, others are beginning to see plastic waste with an entirely different perspective. Our machines are now used almost exclusively for demonstrations. For children, a demonstration is a chance to watch trash turned into unique toys. Kids are shocked to learn that the material from a single one-gallon milk container is more than enough for one injection-mold full-size drumstick. For many adults there is a realization of the amount of work that goes into modern recycling systems. The job is far from over when the recycling truck pulls away from the curb.
We have never bothered to offer products for sale. The labor requirements of running our machines is way too high. And, although usually a point of pride, our machines are a little too junkyard-sourced. We have always been uneasy about the amounts of energy involved. Naively, we jumped in without much consideration for generation of waste water and microplastics with our low-tech processing equipment. After some time, we began to question if the work we were doing was even tangibly helpful at all – even after China rattled the global recycling industry by banning imports of mixed plastics, regional markets for recycled HDPE do still exist. However small our impact, in some ways, our work with clean HDPE served to divert material away from professionals who could do the job better than us.
To be clear, our failure to achieve a reasonable economy is not indicative of the entire Precious Plastics community. Many in developed countries have persisted and developed fantastic niche products. In developing countries, where plastic pollution is much more apparent, these kinds of low cost accessible machines offer real opportunities for entrepreneurs to clean up waterways while making something beautiful. However, on our farm in our part of the world, it was becoming apparent that in order for us to move forward with our work in plastics recycling, we would need to come up with tailored solutions that address our own plastic waste and use much less energy doing so.
Finding Our Niche
Those who have followed us know that we speak often about biochar. We’ve talked a lot recently about various small scale production methods, inoculating biochar for use in the garden, and even touched on water filtration applications for homemade biochar. And even though we’ve been relatively quiet about it, we are still producing biochar with our farm-scale system. At our peak production our ‘triple-retort’ system is capable of manufacturing about ten cubic yards of biochar/week. From 1200 lbs of sawmill waste, a single batch yields about 400 lbs of crushed biochar along with some 40 gallons of wood vinegar, 5 gallons of ‘pyrolysis oil’, and a considerable amount of heat from the combustion of excess syngas. Wood vinegar and oils in the form of raw condensate are stored in second-hand caged HDPE containers known as IBC totes. Over time, tars settle to the bottom of these containers where then clarified wood vinegar can be decanted off the top. We had accumulated a considerable amount of wood vinegar in the years before modifying our system to include a condenser bypass. Scaling up our wood vinegar field trials means a considerable amount of tar-stained IBC totes are left behind. Suffice to say, these tar-stained HDPE totes are too contaminated for conventional recyclers to accept.
Simply put, biochar can be produced when wood, or some other carbonaceous material is heated in the absence of oxygen. This process – known as pyrolysis – requires heat to get started, though after some time it will become self-sustaining. Gases created during pyrolysis can provide the energy to continue the process. In our system, sawmill waste is loaded into large oxygen-limiting stainless steel containers known as retorts. These retorts are indirectly heated, starting at ambient temperature and over the course of a few hours reaching a critical point at which a transformation of the wood waste begins. Some solid material is left behind and carbonized into biochar, while the same time, through destructive distillation gases are released from the heated wood. This blend of gases, known as syngas, exits through a series of pipes where then condensable gases can either drop out as liquids or be directly combusted to provide heat. Through a corresponding series of channels and valves, heat from the combustion of excess syngas can be directed throughout our system and used to start another batch, heat or water, or in our case, recycle plastic.
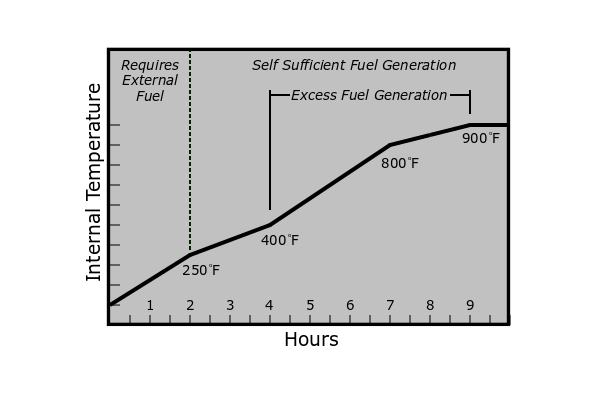
Process time compared to internal temperature of wood in the retort. A five hour window of opportunity for recycling happens between 400 and 900F.
Moving forward with recycling contaminated IBC totes would present a series of challenges. Preparing totes for molding would require removing as much sticky tar as possible from the material prior to shredding. What we found to work best is a process involving removal of the totes from their cages, cutting the bins into strips and laying them out in the sun for weeks. The sun-baked tar is easily scraped off during the shredding process. Still, we needed a larger shredder to accommodate the thicker material. We found luck when a neighboring business sold us a decades-old salvage Weima-WL 6 wood shredder, where then we had it adapted to a tractor PTO drive. Today, shredding the material still remains our biggest challenge.
Our early product designs sought to mimic the versatility of plastic lumber. We built simple steel molds and a large custom press and trials began shortly after. Molds were filled with HDPE chips, loaded directly into one of the retort chambers and indirectly heated until reaching a predetermined optimum temperature. These trials were largely a guessing game at first – and failures were often demoralizing. Plastic would overheat and offgas noxious fumes. Molds were unevenly heated resulting in burned and unmelted sections on the same piece. Even when successful, the shrinkage rate of cooling HDPE was too apparent in the longer board-length molds, causing our finished product to take on a twisting, uneven quality. Nonetheless, we persisted, ultimately concluding 195C was the optimum temperature for compression molding our tar-stained flakes.
The crew addressed the problem with uneven heating by constructing a suspended interior chamber, which could drop into the retort and keep molds suspended above and isolated from overheated surfaces. Air circulation throughout the chamber is maintained with a junkyard-sourced furnace blower. This blower remains powered on throughout the entire heating process. A small setpoint-controlled exhaust blower is utilized to draw in ambient air when necessary to help maintain a more precise internal temperature – in this way, we have both coarse and fine methods for temperature control. Built as a prototype at the time, this ‘convection heater’ has proved effective and is still used today.
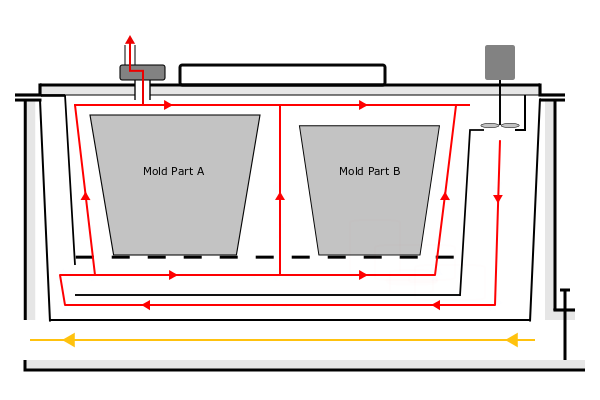
Cutaway diagram of the suspended convection heater. Yellow line represents high temperature gases from combustion chamber to water heater. Red lines indicate circulating air, limited to 195C.
Prior experiments had shown that our method for compression molding HDPE would not produce usable plastic lumber without considerable post-processing – planing, shaping and sanding – all processes that create a demanding amount of fine plastic dust. Additionally these trials proved that a substantial amount of pressure would be required for adequate compression. By the end of 2019, we had built a new, exceedingly robust stainless steel mold and corresponding 20 ton press. Our tree planter mold would handle 28 pounds of HDPE flakes and fit snugly inside our process-heated convection oven. What followed were yet another series of increasingly smaller, but seemingly endless demoralizing losses – we had to build the press even stronger, modify the mold to include a removable bottom, and locate suitable release agents all while continuing experiments with optimizing temperature and residence times. By spring of this year, after nearly a dozen failed attempts at complete tree planters, we had finally dialed in our process.
At ¾” thick, these 18” tall hexagonal shaped tree planters are robust and, in my opinion, quite attractive. Heavy walls and non-structural applications mean we can accommodate contamination to a degree that other more precise molding processes could not. At 28 pounds, we can process a meaningful amount of otherwise non-recyclable plastic – a scale that matches nicely with our stock of material and available process heat. Labor demands are much lesser now during molding and post-processing, but remain high during shredding and washing. Future work will seek to improve on this, and potentially open the door for molding with alternative materials – including LDPE films, and woven polypropylene bags and mulch fabrics.
In Defense of Downcycling
In the fall of 2018 we held an open-house style workshop showcasing our work with plastic recycling. This was right around the time when we were just beginning to experiment with compression molding with biochar process heat. One of the attendees, a recycling industry professional, spoke of a company in the midwest USA that was accepting lower grade agricultural mulch films for recycling into standoffs for interstate guardrails. As someone who commutes via interstate to an agricultural community, I’m often reminded of this comment – a business owner had found a use for all that dirty black film – not in making new film, but in making something entirely different – something downcycled. Downcycling – normally the bane of plastic pollution activists – in this case was the solution. In our case too, our contaminated IBC totes would never be accepted by conventional recyclers forced to compete in quality with virgin material. Downcycling is the only kind of recycling we can do with our expertise, on our shop-made equipment.
A defense of downcycling should not be confused as a defense for the proliferation of single use plastic – What else comes to mind is the absurd distance this lightweight, non-dense material travels to make this transformation. Shipping our plastic waste to China, only to be returned as more single use plastic was an absurd system. It goes without saying we should do all we can to eliminate unnecessary plastic. At the same time, we can be honest about the productive and democratic benefits of durable plastics in our homes and on the farm.
A year later, towards the end of 2019, another visitor to the shop spoke of Dominican locals who would harvest beach plastic and gently heat them while pressing them into blocks. Where others would carve driftwood figurines to sell to tourists, some were beginning to use these mixed plastic blocks as raw material instead.
In my humble opinion, at the time of this writing, those in developed countries wishing to pursue DIY recycling for genuine environmental reasons would do well to be like these Dominican innovators and keep it local and small. They should look to the ideas of the midwestern USA innovators and maintain a narrow, focused approach. And, like both of them, they should prioritize working with conventionally non-recyclable materials.
Questions, Comments, Criticism, Compliments? Send an email