Like everyone else, Living Web Farms is adapting to the changing circumstances of the Covid-19 pandemic. Expanded farm operations and food donations are now top priority. We’ve started a new short-form, rough-edit video series for sharing immediately relevant information and a few weeks ago we offered our first of should be many free webcast workshops. During this workshop I reviewed a number of different low-tech point-of-use water treatment technologies and quickly introduced some exploratory work with production of activated carbon from our wood-waste sourced biochar. Today, for the blog, I’ll take a closer look at activated carbon and how it’s made and used around the world for removal of chemical contaminants from drinking water.
Household Water Treatment
In 2015 the World Health Organization estimated that 2.1 billion people do not have safe water at home and of those, 159 million still primarily drink water from untreated surface sources such as streams and lakes. Surface water is rarely fit to drink unless clarified and treated for the removal of biological and chemical contaminants.
Diarrheal diseases as a result from consuming microbiologically contaminated water are a severe and immediate human health concern. An often cited WHO publication estimates that 2.2 million people die every year from gastrointestinal infections. Tragically, young children are especially at risk of life threatening cases of diarrhea and further developmental issues related to malnutrition in non-lethal cases. The good news is these diseases are largely preventable – and much attention has been paid to providing appropriate microbiological water treatment technologies to those in developing countries, ranging from the no-tech SODIS method, to locally produced biosand and ceramic pot filters, and beyond to the more recently developed higher tech personal use Steripen UV device and Madidrop tablets. The downside is that, for the most part, these technologies do very little for treating water for chemical contamination.
Chemical contaminants may range from those that are naturally-occurring like arsenic, radon and fluoride, to lead in aging municipal water systems, or to the more complex and insidious herbicides, pharmaceuticals and industrial pollutants. Interestingly, arsenic can be mitigated with locally-made iron-modified biosand filters and fluoride can be removed by passing water through calcium-rich bone char – However, altogether broad chemical decontamination of point-of-use drinking water is typically done with one of two technologies: removal via reverse osmosis or adsorption with activated carbon.
Biochar and Activated Carbon
If you’ve followed any of our work, then you’ll know we speak often about the physical properties of biochar. Well-made biochar is resistant to decay, has a well-developed pore structure, and a high internal surface area. These properties are what makes biochar work so well in building soil fertility – nutrients will ‘stick’ the internal walls of the charred material and diverse microbes can inhabit the open pore spaces. Well inoculated biochar in the soil helps maintain a thriving soil ecosystem in the midst of external pressures such as tillage, drought or excess fertilizing. In this way it can be even used as a vehicle for restoring fertility to damaged, lifeless soils.
One could think of biochar inoculation as essentially filtering a nutrient rich solution. For example: If fresh, raw biochar is added to a bucket of tea made from rich worm castings, the nutrients will be drawn in and adhere to the internal walls of the porous char. One could now think of the tea itself as partially filtered. Extrapolate from here and things get more interesting: biochar can be used in a cascading manner – for example, first as a filter adsorbing excess nutrients from the floor of the chicken coop, then to in the compost to maintain moisture stability and low bulk density, and lastly to its final destination in the soil. Biochar could be used to filter water contaminants too, although it should be mentioned: careful attention should be paid to what is being filtered and whether or not it is acceptable to accumulate and bury these contaminants.
Before moving on, lets review a few definitions:
- Biochar is essentially an agricultural or forest waste-based charcoal that is destined for the soil with the intention of building fertility. This is an important distinction when marketing the material, as biochar is usually processed at higher temperatures than regular charcoal, sieved, and sold in pre-inoculated compost blends.
- Charcoal that is intended for cooking might be processed at lower temperatures, leaving behind compounds that help it light easier and give its characteristic charcoal flavor.
- Filter charcoal should be processed at high temperatures, as to remove all possible pore clogging tars and maximize usable surface area. Typical filter charcoal is a select biomass that has undergone pyrolysis, but has not been Activated.
- Activated carbon is like filter charcoal, but further processed to increase internal surface area. Activating charcoal is distinctly different from Incoculating or Charging biochar.
The first documented case of charcoal as a filter substance hails from around 1500 BC when ancient Egyptians used it to absorb odors when dressing wounds. Around 400 BC, Phoenicians would store potable water in charred barrels on their trading ships to ‘improve taste’. But it wasn’t until the late 18th century that scientists began to understand charcoal’s adsorptive properties. In 1913 French chemist Michel Bertrand dramatically swallowed a lethal dose of arsenic, followed it with charcoal and survived. A few decades later, another French scientist would publicly perform a similar demonstration by swallowing strychnine and charcoal in front of the French Academy of Sciences (he was however apparently booed off the stage). In 1903, inventor and ‘subject of the Emperor of Russia’ Raphael Ostrejko was granted the U.S. patent for a ‘process of obtaining carbon of great decolorizing power’. What he was describing was carbon with an improved adsorption capacity – produced by applying controlled steam over red hot charcoal – that would eventually be known as activated carbon.
Activated Carbon
Today, activated carbon production is a multi-billion dollar enterprise supplying material to a broad range of industries. It can be found in numerous consumer products from gas masks to posh cosmetics. It can be found in hospital emergency rooms, electro-plating facilities, distilleries and water treatment facilities. Modern activated carbons are produced in a number ways, usually under specific parameters for targeted end-use applications. All activated carbons are characterized by well developed pore structure and high adsorptive capacities – some may be chemically treated or ionized to target specific pollutants. Our interest here is in granular activated carbons for water purification. They are generally produced in one of three ways:
- Physical Activation – Charcoal is produced, sieved to specification,heated to 800-1100C and then steam, carbon dioxide gas, or some other oxidizing agent is carefully applied, creating additional fractures and tiny micropores along its internal mesopores.
- Chemical Activation – Prior to carbonization, biomass is milled and chemically pretreated – possibly with potassium hydroxide or phosphoric acid, or a salt such as zinc chloride. Activating agent is chosen based on biomass properties and desired chemical qualities of the end product. Lower temperatures are required for activation, but chemical activation can be very corrosive to pyrolysis equipment.
- Physio-Chemical Activation – Charcoal is produced, sieved, and then chemically activated and heated to a high temperature.
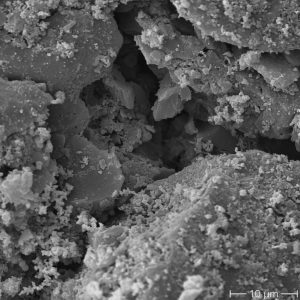
SEM photograph of Activated Carbon Source
In water treatment applications, activated carbon is mostly used for the removal of natural and synthetic organic compounds including, but not limited to chlorine and disinfection byproducts, industrial chemical pollutants, and some relatively harmless, naturally occurring compounds that negatively affect odor and taste. This works mainly through physical adsorption – molecules are drawn in via intermolecular forces and then stuck to the massive internal surface. One could think of this is a weak magnetic force, or similar to adhesion like dust on tape. If considering granulated active carbon for a water purification project remember:
- Contaminants must be in extremely close proximity to the carbon for adsorption to work. Contaminated water should not be allowed to bypass the filter media. For this reason, dense packed filters are better than loose ones.
- Adsorption improves over time. Slower water flow rates through the filter medium are generally more effective. For this reason, gravity fed systems are generally more effective than pressurized ones.
- Contaminants will occupy available surface area and build up over time. Eventually this surface area is no longer available and some contaminants will bypass the filter.
- Breakthrough is described as the point at which the filter is no longer effective at keeping specific contamination levels under acceptable limits.
- Well designed carbon filters factor in reasonable breakthrough points for various pollutants and acceptable flow rates.
- Activated carbon filters can be designed to be more effective at holding some contaminants than others – the breakthrough point of the contaminant with the lowest affinity determines the filter’s ‘expiration date’.
The science of activated carbon is complex, and it’s understood that I shouldn’t expect to be able to make gas-mask or pharmaceutical grade carbon in my backyard over the course of a weekend. Nonetheless, perhaps out of ignorance, arrogance or genuine curiosity – or some inspiration by the 19th century French scientists who risked their lives for science – I set out to explore whether it was feasible to make filter-grade activated carbon from our biochar at Living Web Farms.
DIY Activated Carbon
In late winter of this year I set out to explore what it would take to make granular activated carbon (GAC) from our biochar. My ultimate goal was to have a material suitable for the adsorption of any potential hazardous chemicals in my rainwater collection system. At my home I have a simple food-grade IBC tote and repurposed barrel collection system that retains water collected from asphalt shingles, aluminum gutters and flexible PVC piping. 400 gallons of storage means I can handle irrigation needs for up to a few weeks, and still have backup domestic water for the times when my aging community well system goes down for maintenance. Incoming rainwater is almost always cleaner than surface water – although one must consider the roof itself is a surface of its own. I would need a system that allows for settling of particulate matter, simple filtration, microbial deactivation (I’ll be using chlorine for residual protection) and protection against potential organic compounds and chlorine byproducts. Now I use the popular Berkey brand carbon block filter system – in the spirit of self-reliance, for future experimentation I’ll be using a refillable canister filter and allowing for the longest possible filter contact time.
For our experiments in activated carbon production I took inspiration from the immensely popular Cody’s Lab YouTube channel. Cody does a great job in his video explaining activated carbon, where he then goes on to produce a small amount of steam-activated material in an electric induction oven and follows it up with an iodine test to compare its adsorption capacity to store bought material. My plan was to perform a similar experiment, using our hardwood biochar as a feedstock, screened and heated with LP in the standalone refractory chamber our team built when developing our atomizing pyrolysis oil burners. At the same time I set out to compare the adsorption capacities of several ‘DIY’ chemically activated chars, this time, following the recipes provided by several other popular youtube and survivalist-themed blogs. Unactivated char produced in my TLUD cookstove was also compared. Adsorption capacities of the final products were to be compared with two simple tests: (1) via visual indication of methylene blue adsorption and (2) following the R-134a adsorption procedure as described in chapter 8 of the Biochar Revolution.
Samples were prepared:
- Enough retort-made biochar for several tests was screened to <1/8” and >1/16”, rinsed and dried at 350F for 2 hours.
- TLUD char was similarly screened, washed and dried.
- Canning jars were filled with the uniformly dried, granulated material and sealed until activated.
I proceeded to test several DIY chemical activation methods, following guidelines set out by popular DIY and survivalist-themed blogs:
- A 4 oz. jar of prepared char was covered in 3 oz. of lemon juice and covered overnight.
- 30mL of calcium chloride was dissolved in 100mL of distilled water. This mix was poured into a 4 oz. jar of prepared char and stirred to paste consistency.
- A potassium hydroxide sample was prepared similarly.
- A wood-ash sourced potassium carbonate sample was prepared similarly.
- All jars were covered and allowed to sit for 24 hours. After which they were well rinsed over a stainless steel screen and oven dried for 2 hours at 250F.
In the meantime, a vessel was built for applying steam to heated char. Again, taking cues from Cody’s lab, I knew it was important to distribute steam evenly, for a short time across a column of heated granulated material. The vessel would need to accommodate a volume of sacrificial char in order to prevent any excess oxidation during heating. Two samples were prepared, a steam activated sample and a heated, non-steam activated sample. Both samples were slowly brought up to 1800F and held there for 1 hour. Distilled water was simultaneously heated in a cast iron teapot. Steam was generated and applied in 2 minute increments for a total of 10 minutes over 20 minutes time. Samples were allowed to cool and stored in canning jars until testing.
All samples were stored in canning jars and labeled as follows:
-
- Control – Retort biochar, carbonized at 850F for at least one hour.
- TLUD – Char generated in a gasifying cookstoves.
- High Heat – Retort biochar, heated to 1800F for one hour.
- Steam – Retort Biochar, heated to 1800F and steam applied for a total of 10 minutes.
- Commercial – A store bought granulated aquarium filter carbon.
- KOH
- CaCl2 – AKA “Pickle Crisp”
- K2CO3
- Lemon
30 mg samples of each carbon were measured into 35 mL test tubes and covered with 30mL of 1% methylene blue solution. Samples were gently stirred, covered and allowed to sit for 24 hours.
After 24 hours there was some visible change, but I wanted a more nuanced look. 30 mg samples were similarly prepared with a .25% methylene blue solution. By this point I had run out of commercial activated carbon.
In the meantime, samples were compared with the R134a test as outlined in Chapter 8 of the Biochar Revolution. In this process, a known weight of char is loaded into a small vessel and swept with a heavy refrigerant gas. The adsorption capacity is estimated by the weight gain of the sample. The end point of the adsorption reaction is determined by a temperature change – the char sample heats up during adsorption, followed by a temperature drop when it reaches capacity. I had some trouble determining this point – ultimately it took three cans of refrigerant until I was confident it was done. Nonetheless I proceeded to compare the before-and-after weights of my remaining samples:
Conclusion
The steam applied char performed well in the methylene blue test. There was little difference between control and high heat chars. All chemical-activated samples performed poorly – in all cases worse than the control char itself. Simply applying a strong base, acid or salt to the char and rinsing does not work to create activated carbon – in time, I’ll attempt a proper physio-chemical activation by heating these chemically activated samples up to 1800F and compare again. For now, it’s safe to say that the chemical activation methods repeated on many YouTube and blog posts are not helpful in improving the adsorption capacity of proper charcoal. It is possible they help to some degree in improving low heat, tar-clogged chars, but it is doubtful the result is anywhere near what may be considered activated carbon.
The TLUD char was the star of the show – It compares surprisingly well, and given enough time, with the naked eye it appears to perform nearly as well as steam or even better than commercial activated carbons. This confirms the rule that higher filter contact times make for more effective filtration. These results are especially exciting given that TLUD char production requires no additional energy input and is much less demanding of my labor. I look forward to testing again with TLUD production methods combined with chemically activated biomass – I’ll start by soaking hardwood chips in a solution of wood-ash sourced ‘lye-water’.
Since performing these experiments I’ve come across the work of Dr. Joshua Kearns and the work of Aqueous Solutions. This is exciting stuff – their team is researching and developing extremely low-cost, locally-constructed, multi-barrier water treatment systems that include high-temperature biochars for removing chemical contaminants. Kearns’ peer-reviewed work has been shared with the International Biochar Association and CAWST – Open source plans are available here. What’s most exciting is that this work confirms high temperature biochars – those made with improved (still simple, still locally made) TLUD style methods – perform nearly as well as the ‘gold-standard’ activated carbons for adsorption of a variety of common surface water pollutants. Essentially, according to his research, there are no major differences in the feedstocks tested, but rather the difference is in production method – gasification chars, made with high temperature methods perform much better than lower temperature kiln-produced charcoal for control of organic chemical pollutants. Activated carbons ultimately still perform better for adsorption, but when compared to char that can be locally made with agricultural wastes on low tech production equipment, the cost/benefit analysis doesn’t always check out.
Want updates? Questions answered? Comments and criticisms? Send me an email.