Part One available here
The nexus of appropriate technology, circular economy and agriculture is a buffet of challenging, interesting projects. In 2017 and 2018, our continued work in biochar and gasification, and among other esoteric projects, our work with small-scale plastic recycling, – not to mention organizing the WNC Repair Cafe project – have kept us pulled in many directions. With so many new frontiers, when we’ve got a minute, its nice to get back to something we’re becoming quite comfortable with: our Babington style pyrolysis oil burner.
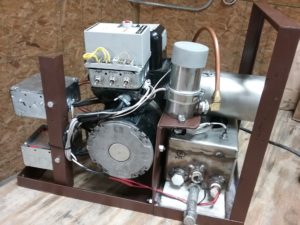
We’ve modified our previous pyrolysis oil atomizer to fit in a smaller package. Note the manual override controls for servicing, and the smaller sump is required to interface with our biochar equipment.
Pyrolysis oil
Think of what we call pyrolysis oil as somewhat interchangeable with what is sometimes called ‘bio-crude’ or simply tar and ‘creosote’. Though the common definition of creosote (at least in the southeast USA) tends to encompass all wood liquids, it’s usually brought up when talking about build-up in a wood fired chimney. This gooey/sometimes crusty mess lining your chimney is basically condensed smoke from a smouldering fire – the product of cold and partial combustion. Pyrolysis oil is a little different: its produced by condensing the gases released during pyrolysis – something that all happens prior to the introduction of oxygen. Its also important to note here that wood creosote is different than the inherently more toxic coal tar creosote that throughout the 20th century was commonly used as a wood preservative. So as to avoid confusion, instead of calling it creosote, we’ll stick to calling it tar and pyrolysis oil.
Plant based tars and oils have a well documented long history of use in pre-industrial shipbuilding – tars worked well to seal the joints and prevent rot on wooden hulls. Some historians have claimed that for a period during the 18th and 19th centuries that North Carolina (go Tarheels!) led the world in production of pine tar and turpentine. Lesser known is its role in early road construction (see: tarmac), roofing, and and interestingly, in varying degrees of legitimate and quack medicines like tar water. (If you’re curious, the story of philosopher and UC Berkeley namesake George Berkeley’s obsession with tar water is certainly a bizarre one.)
These days, with pyrolysis emerging as a viable waste management tool for tires and plastics, along with farm and forest wastes, its possible that these wide ranging pyrolysis liquids may re-emerge as a major contributor to the peak-cheap-oil chemical industry. Plastics to fuel technology is getting a lot of attention, and biomass tars in bio-asphalt appear to be performing well as a suitable alternative to conventional petroleum binders.
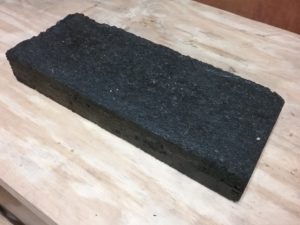
The crew at LWF Biochar made this block of asphalt using a conventional aggregate ratio while replacing petroleum based binders with wood tar. Though it doesn’t see normal wear conditions, it has been left in the sun, rain and snow for a few years now.
Pyrolysis condensates vary greatly with differing feedstocks and processes. Ours is derived from mostly high-lignin Appalachian hardwood mill waste, resulting in a molasses thick, oxygen and water rich, very sticky and highly acidic complex oil/tar blend. I’ve wrote before about we use pyrolysis oils as a consistent and meterable, stable liquid fuel. These advantages of liquid fuels over other renewable alternatives are definitely attractive, and though clean combustion of pyrolysis oils is challenging, we believe we’ve found a suitable solution with the babington ball nozzle design.
Babington Style Burner, Revisited
A year ago when I wrote about our first-generation babington style burner, I left off with remarks about what kind of improvements we’d like to make. Our first unit was large, with a clunky preheat system, awkward controls and unreliable (and honestly, a bit dangerous) ignition system. We’re by no means done with our work, but we’ve come a long way since then. Our new unit is mostly squeezed into a conventional gun style burner housing. It sits low enough to the ground now that it interfaces with our biochar production equipment. We can preheat in ⅓ of the time and auto-fill the sump from a 20 gallon vessel for (theoretically) up to 20 hours continuous burn time. Start-up is much more reliable, and perhaps most importantly, atomization is adequate for continuous +900C combustion. There’s still plenty of work to be done with (to name a few) improved float controls, emissions testing, weatherproofing and cold weather operation. Despite the issues, I’m confident we’re not far from this machine serving as our primary startup heat source for biochar production – where we may be able to eliminate our wood chip gasifiers entirely – trading one source of (debatedly) carbon neutral heat for one that, when considering sequestered biochar, could actually be called carbon negative.
If you’re like most people investigating oil burners , you’ve already got a source of waste motor or vegetable oils. For these fuels, there are plenty of commercial waste motor oil burners available. If you want to see one in action, there’s a good chance you can see one at any of the common drive through oil change shops. Most of these burners can swap between motor and vegetable oils, so long as attention is paid to proper filtration and a means to adjust heat is available. Remember, compared to conventional oil burner nozzles, siphon nozzles have slightly larger passageways and allow for some leeway in fuel quality. Though if you’re like us, and your fuel demands a low degree of filtration, nothing beats the Babington ball nozzle design – where fuel is spread over the nozzle, not through the nozzle as in other designs. Another important detail: conventional waste oil burners require robust air compressor systems to achieve atomization and drive the siphon fuel delivery system. Babington style burners still require compressed air, but the volume is much less due to the very tiny hole on the nozzle. Our unit has a (comparatively large) .0137” hole and has proven to work (where others have not) on the volume of air available from typical junkyard sourced refrigerator compressors. Admittedly, this isn’t the safest, and certainly isn’t suitable for long term operation, but it is a decent tool for demonstrating the relatively small amount of compressed air actually required.
[tribulant_slideshow gallery_id=7]
Just like last time, I’ll leave with a few notes on improvements. Improved float controls and overflow alarms are the first to come – there is a delicate balance with this small sump and overflows are messy and dangerous. If not for buildup in the long burn tube our run time would likely be limited only to the volume of fuel in our preheat tank. Modifying the burn chamber inlet tube will possibly fix this; for improved atomization smaller nozzle holes and a true ball design can’t hurt. A dedicated shroud with engineered cooling air will keep electronics cool, contain catastrophic fires and allow us to operate in rainy weather. There’s still work to be done.
Before we finish: A reminder about safety. Though we love to read and hear stories and share our experience experimenting with alternative fuels, it should be noted the system we’ve designed and shared here is experimental and optimized for our specific blend of hardwood tars and oils. We never encourage modifying a furnace for waste oil operation, and we don’t endorse leaving DIY machines to operate indoors without constant supervision. Be safe – saving a few dollars is nice, but its never worth the risk to people and property.
As always, feel free to reach out to us for questions,
|