Update: 10/26/18. Part 2 available here
Summer HVAC season is coming to a close and lately our local scrap-yard has been teeming with old oil burning furnaces. While Asheville residents are replacing oil burners with updated heat pump systems as fast as they can, conscious builders and tradesmen are recycling the used equipment, and although many of these machines are fully functioning, no doubt many of them still end up at the landfill. What can be done to keep this robust, sometimes outdated, technology out of the waste stream and put to good use? The biochar crew at Living Web has been working over the past year to develop oil burning technology for clean combustion of pyrolysis oil – a corrosive, sticky, and heavy liquid coproduct of biochar production.
Conventional Oil Burners
Conventional oil burners are commonly found in older homes and in areas where heating systems were installed prior to the widespread availability of natural gas. They’re the appliance commonly found in basements, that pulls oil from a large tank, and burns it in a chamber housed directly underneath a furnace or boiler. These home heating oil (HHO) burners are set up for a specific grade of oil, commonly referred to as #2 fuel oil (Imagine the viscosity of diesel fuel). In fact, any oil furnace designed for #2 fuel oil can accept up to 20% biodiesel with no modifications. WNC locals may be familiar with bioheat from Blue Ridge Biofuels – a blend of up to 20% biodiesel and fuel oil. For those of you outside of the area with oil furnaces and boilers in your home, use this map to find biodiesel distributors in your area. Also, see the Dept of energy site for suggestions of some simple procedures, such as nozzle resizing, that can cut up to 10% off fuel usage.
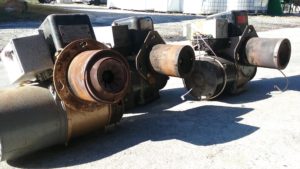
These “gun style” burners were pulled out of old furnaces instead of getting crushed at the the junkyard. Conventional oil burners can be modified to accept a wider range of fuels to provide intense heat for many processes.
How do they work?
Conventional oil burners are a tightly packaged system of components: oil pump, blower, nozzle, ignition system, controls and safety mechanisms. These ‘gun-style’ burners work by forcing refined oil through a specialized nozzle at high pressure, creating a mist that ignites in the presence of a high voltage spark. This extremely fine, or atomized, spray facilitates clean combustion by reducing the particle size of fuel relative to combustion air. Think about kindling when starting a campfire – given adequate combustion air, small pieces of wood burn quick, clean and hot – It’s the same with an atomized spray. The right amount of oxygen is introduced, add spark, and the resulting flame is then managed in a burn chamber, where the intense heat is directed across a heat exchanger, warming the air or water in a residential heating system.
Apart from improvements in flame retention and combustion air handling, very little has changed with the gun style burner in decades. Of course, environmental and resiliency issues arise when considering the extraction and distribution of our remaining cheap petroleum, especially when it’s diverted to home heating use, where there are so many better options. However, operation of these burners is surprisingly clean, they have to be, or soot clogs the small passageways in a typical furnace heat exchanger.
There are a few more things that make these working with these conventional oil burning technologies so interesting:
- Liquid fuels inherently have certain advantages: they’re easily stored and metered for predictable power output. This is essential in certain of kinds of equipment, and merely a convenience in others.
- Clean combustion requires high temperatures – an advantage when applied correctly. High temperature heating fuels are not always necessary in a home heating system, but are critical when applied in certain applications, such as backyard foundry or ceramic kiln.
- Unless otherwise indicated, gun style burners are designed to only burn #2 fuel oil (and up to 20% biodiesel). Higher concentrations of alternative fuel oils require equipment modifications. Fortunately, these modifications are well documented: waste motor and vegetable oils are accessible fuel alternatives.
Retrofitting a gun style burner for alternative fuel use requires a few distinct changes to the original design. Specialized siphon nozzles use compressed air to deliver fuel spray while preventing clogging issues and eliminated the need for the oil pump. Waste motor oil has a higher flash point than #2 HHO and requires additional fuel preheating. We use a small (surprisingly affordable) PID controlled heating element at the nozzle for reliable startup and consistent operation. The details go on, and these are not easily understood modifications without a little background and tenacity. Lucky for us, CKburners provides kits and detailed instructions for those starting out. For our first unit, we bought the block heater and siphon nozzle kit. For those inclined to sourcing salvaged materials, one could be able to modify an existing oil burner with this kit for as little as $400.
Pyrolysis oil
At Living Web Farms, our end goal was a machine not limited to the use of waste motor oils, or even used vegetable oils. We needed a system that could reliably burn pyrolysis oil – a coproduct of our slow pyrolysis method of biochar production. In slow pyrolysis, gases are released from dry biomass as it’s heated in the absence of oxygen. These gasses pass through a condensing unit on their way to a controlled burn chamber. At the condensing unit, gasses that can be condensed drop out as liquids, where they drain into large holding containers. Over the course of a few months, heavy oils and tar settle out in the bottom of these containers. The lightest of these oils are what we call pyrolysis oil, which is separated and stored for use as fuel. The remaining liquid products, tars and wood vinegar (or, pyroligneous acid) are also separated at this time, where it’s stored and used later for all sorts of interesting things.
Pyrolysis oil has some very different qualities that set it apart from conventional fuel oils. It requires fine atomization into a hot burn chamber. It’s highly corrosive, and its viscosity changes dramatically with changes in temperature. From our experiments, we’ve learned if it’s heated beyond a certain threshold, it won’t return to a liquid form. Since then, we’ve learned this may be due to increased oxygen exposure, and this makes sense too, as if it’s allowed to dry in the sun long enough it can create a hard plastic like shell. These characteristics become distinct challenges when tasked with designing an appropriate burner. Because of these issues, especially corrosivity and clogging problems, we knew it wouldn’t be reasonable to ‘push’ pyrolysis oil through the tiny passageways in the nozzle of a modified gun style burner. Our research in DIY metal casting brought us to the babington style burner.
The Babington style burner
Babington burners were developed in the 1970’s by the inventor, Robert Babington, as a means of achieving very fine atomization spray at low firing rates. Babington Airtronic burners saw an early market in the 1980s as home heating units in mostly European households. Today, the technology has been picked up by the US military in remote cooking applications. Babington burners have a unique ball-shaped nozzle design that not only provides a fuel efficient burn, but also allows for a much wider range of fuels, requiring much less filtration than modified conventional burners.
The heart of the babington burner system is the ball shaped nozzle. Instead of forcing oil through a nozzle with a pump, now, oil is pumped over the ball, where it forms a thin film as it stretches out over the surface of the ball. At the equator of the ball, where the film of oil is at it’s thinnest point, it intersects a stream of pressurized air forced through a very small hole. Atomization is achieved here, where the fine spray of oil passes near an ignition point, more air is introduced, and clean combustion is realized. Excess oil flows over the ball and back into a vessel (sometimes called a sump) where it is continuously pumped back over the ball. The original babington burners were designed for high efficiency, low firing outputs. DIY builders have experimented with ways to adjust heat output (and thus, fuel consumption) by adjusting the size and number of holes in the ball, flow rate of oil, and pressure of air through the nozzle.
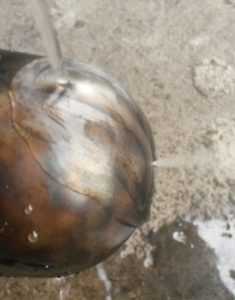
Water poured over a ball shaped nozzle as air passes through a very small hole produces a very fine spray
At normal temperatures, our pyrolysis oil is too thick for filtration through standard oil filters. For us, the real advantage of the babington style nozzle lies in the reduced need for this level of fine filtration. Since our oil won’t be forced through a conventional nozzle, the fuel only needs to be filtered to the extent that it can be pumped. Our system uses a 12V gear pump to deliver oil from a salvaged LP tank sump onto a stainless 2” ball with a .03” hole. Preheat is applied to the entire reservoir through a copper coil heat exchanger, where heat is drawn in from either a very small DIY electric water heater, or off the excess heat generated from the system. Conventional electrodes and ignition control are sourced from another scrap yard burner. With this setup, we’ve achieved very clean combustion of pyrolysis oil, at temperatures up to 2000°F in our burn chamber, on very little fuel consumption (½ Gal/hr).
Our burn chamber was built with a modular design in mind. Either the babington style burner or our modified gun-style burner mount on a flange on the inlet tube. The burn chamber functions as a crude kiln or foundry with a modest amount of temperature control. The lid removes easily to reveal a universal flange for mounting a water heater, or for accommodating future appliances like a tumble dryer or forced air furnace. Things get interesting here, where we can maximize efficiency by stacking appliances. For example, simultaneously we can melt aluminum in the chamber, while heating water, and then sterilizing growing media or drying wood chips, before exhausting through the flue.
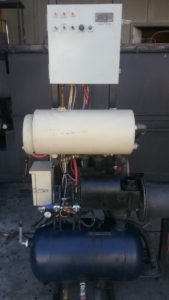
Our babington style pyrolysis oil burner: this thing is tank! Built with experimentation in mind, we’ve demonstrated pyrolysis oil can burn clean and hot.
We built our first babington style burner with experimentation in mind. Honestly, It’s an oversized unit that leaves much to be improved upon. The preheat system is clunky and requires too long for the system to start from cold. Our conventional ignition system isn’t reliable with oils it wasn’t designed for. Overall, there are too many ways this system can fail. Even with our automated safety controls, this isn’t a machine you would want to walk away from for long, much less leave overnight for greenhouse heating.
For me, it’s not until you pick something apart and start rebuilding that you gain an appreciation for the original. This winter we’re looking forward to redesigning our babington style burner. We’ll try to fit it all into a conventional gun style burner package. Our new system will start reliably (and save energy) by preheating the oil only at the point before flows over the ball, and we’ll include an LP source for cold starts, and possibly lose the conventional ignition source all together. We’ll be developing more low cost applications for the heat: greenhouse heating, plastics recycling, feed processing and more.
Stay tuned, we’ll be updating our progress on the blog. As always, send me an email if you’d like to know more.
Update: 10/26/18. Part 2 available here